
1. Incoming raw materials inspection All incoming materials: drums, toner, blades, PCRs, magnetic rollers, etc. are verified against stringent standards before they reach the production floor.

2. Sort & GradeAll empty cartridges are sorted and graded. Only premium empty cartridges are used to ensure optimal quality.
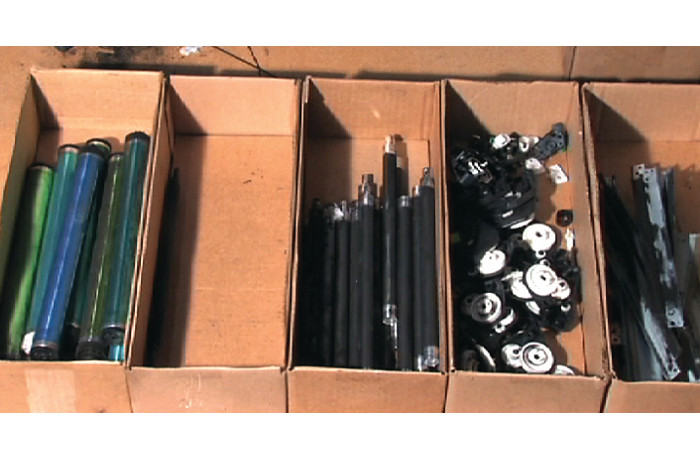
3. RecycleAll packaging materials, used hoppers and non-conforming components are disassembled and recycled.
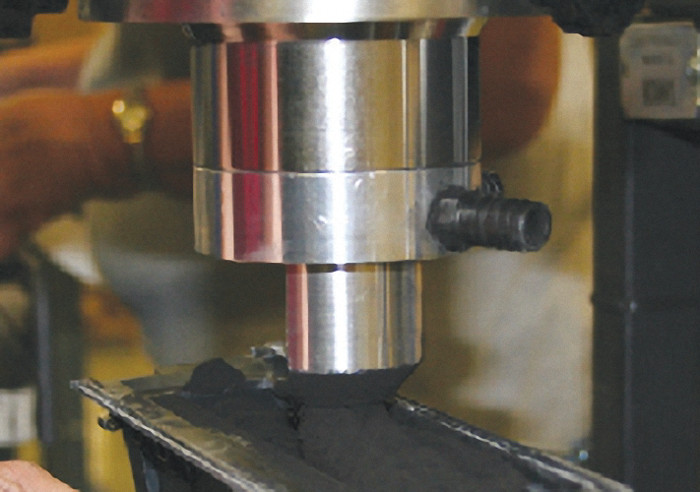
4. Split & CleanEmpty cartridges are carefully disassembled and cleaned using a proprietary state-of-the-art process. Hopper's are precisely split using custom built automated equipment.

5. Digital Auto FillingUsing automated filling equipment that we develop in-house, each cartridge is precisely filled to the exact specified weight. Toner hoppers are filled with premium toners, which are technically matched to the OPC's (drum) for optimal yields and printer performance.

6. SealingEach toner hopper is sealed withan OEM style seal. Our quality sealing process ensures a leak-proof cartridge that is easy for the consumer to install.

7. AssemblyOur factory-trained technicians assemble all cartridges with OEM grade compatible components (up to 75% new components are used in each cartridge.) The assembly process includes the installation of a pre-qualified drum, wiper blade, doctor blade, PCR and magnetic roller.

8. 100% Post TestingEach and every cartridge is post tested utilizing industry standard print tests to ensure outstanding performance and quality.

9. PackagingAll cartridges receive a final inspection to ensure they conform to our stringent quality standards. Cartridges are cleaned, polished, heat-sealed in a static resistant bag and boxed. A full set of instructions and warranty information is included.

10. Quality ControlEach step in our manufacturing process is monitored by dedicated Quality Control experts. Each step in our production process undergoes regular and spot inspections to guarantee that our products meet the expectations of the consumer.

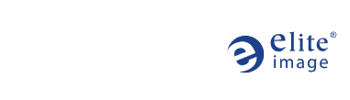